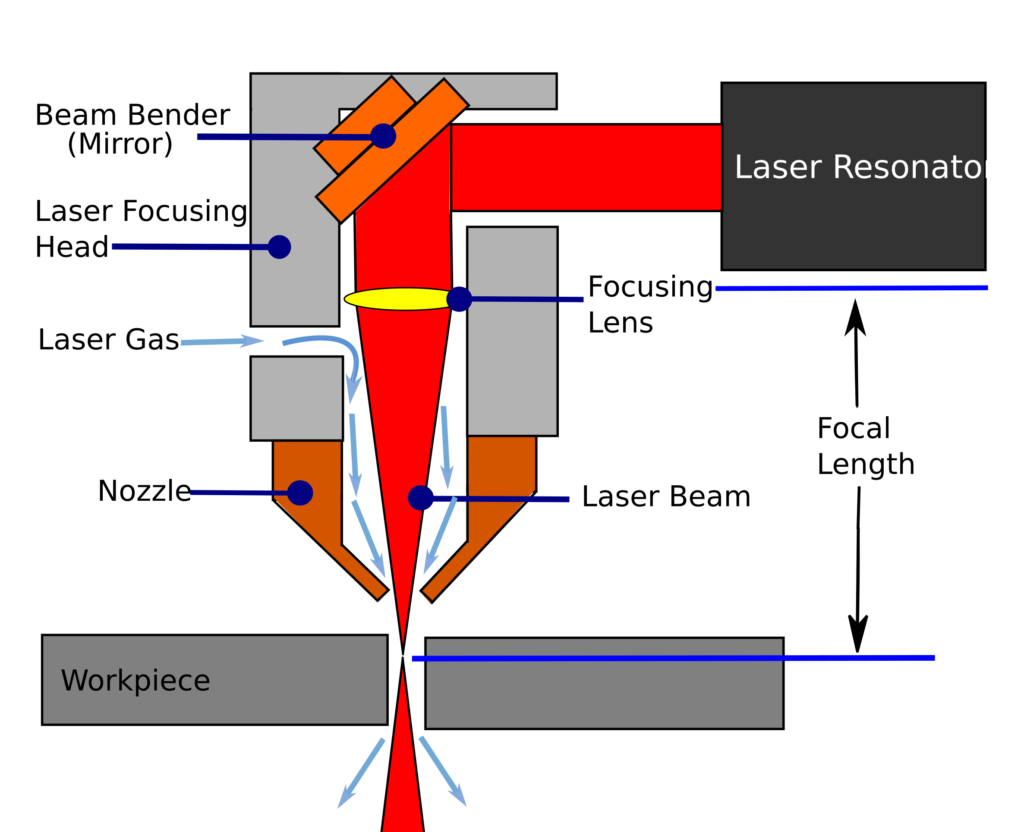
Das einfache schematische Diagramm des Laserschneidens ist in der folgenden Abbildung dargestellt. Während des Prozesses muss Hilfsgas verwendet werden, um die Schlacke in der Schnittnaht wegzublasen, die Oberfläche des bearbeiteten Objekts zu kühlen, um die erhitzte Fläche zu reduzieren, und die Linse des Laserkopfes zu kühlen und zu schützen. Zu den Hilfsgasen gehören im Allgemeinen Sauerstoff, Stickstoff, Druckluft usw., die sich direkt auf die Schneidleistung, die Schnittgeschwindigkeit, die Schnittdicke usw. auswirken. Je nach Unterschied bei den Schneidmaterialien müssen unterschiedliche Hilfsgase verwendet werden.
1. Sauerstoff als Hilfsgas

Sauerstoff wird häufig zum Schneiden dickerer Kohlenstoffstahlmaterialien verwendet. Da die Wärme der chemischen Reaktion mit Eisenelementen das endotherme Schmelzen des Metalls fördert, kann die Schneideffizienz erheblich verbessert werden. Sauerstoff führt jedoch dazu, dass das zu schneidende Material einen deutlichen Oxidfilm auf der Endfläche des Schnitts erzeugt, und erzeugt außerdem einen Abschreckeffekt auf das Material um die Schnittfläche herum, wodurch die Härte dieses Teils des Materials erhöht wird wird einen gewissen Einfluss auf die spätere Verarbeitung haben. Das Schnittende sauerstoffgeschnittener Materialien verfärbt sich schwarz oder dunkelgelb. Im Allgemeinen werden Kohlenstoffstahlplatten mit Sauerstoff, Niederdruckbohren und Niederdruckschneiden geschnitten. Sauerstoff wird im Allgemeinen aus flüssigem Sauerstoff verdampft, der von Luftzerlegungsanlagen bereitgestellt wird, sodass die Qualität der Gasquelle sauber ist und keine spezielle Behandlung erforderlich ist.
2. Stickstoff als Hilfsgas
Wenn Stickstoff als Hilfsgas zum Schneiden verwendet wird, bildet es eine Schutzatmosphäre um das geschmolzene Metall, um eine Oxidation des Materials zu verhindern, die Bildung von Oxidfilmen zu vermeiden und ein oxidationsfreies Schneiden des Materials zu erreichen. Allerdings ist die Schneidfähigkeit nicht so gut wie die von Sauerstoff, und der Stickstoffverbrauch beim Stickstoffschneiden ist höher und die Schneidkosten sind höher. Die nicht oxidierte Schnittfläche weist die Eigenschaften von Direktschweißen, Lackieren, starker Korrosionsbeständigkeit usw. auf und die Schnittendfläche ist weiß. Stickstoffgas wird im Allgemeinen zum Schneiden von Edelstahl, verzinkten Blechen, Aluminium und Aluminiumlegierungen, Messing und anderen Materialien verwendet, wobei zum Lochen niedriger Druck und zum Schneiden hoher Druck verwendet wird. Beim Stickstoffschneiden haben Änderungen im Gasfluss einen großen Einfluss auf das Schneiden. Bei der Sicherstellung des Schneidgasdrucks muss auf einen ausreichenden Gasfluss geachtet werden. Stickstoff wird im Allgemeinen aus flüssigem Stickstoff verdampft, der in Luftzerlegungsanlagen bereitgestellt wird, sodass die Qualität der Gasquelle sauber ist und keine spezielle Behandlung erforderlich ist.
3. Druckluft als Hilfsgas
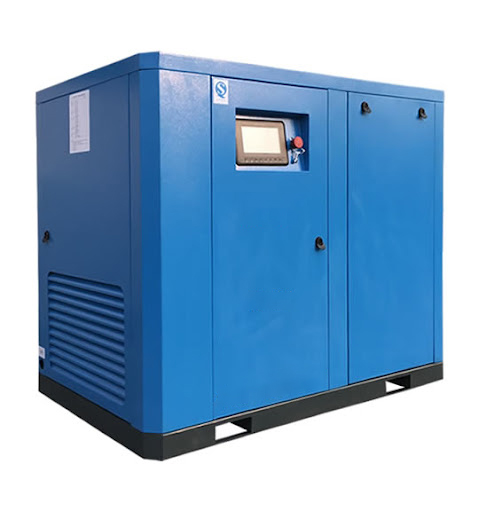
Druckluft ist leichter zu bekommen als Sauerstoff und Stickstoff und sehr günstig. Luft enthält etwa 20 % Sauerstoff und etwa 78 % Stickstoff. Die Schneideffizienz ist weitaus geringer als die des Sauerstoffschneidens, aber die Schneidfähigkeit kommt der von Stickstoff nahe. Die Schneideffizienz von Luft ist etwas höher als die von Stickstoffschneiden. Durch die Anwesenheit von Sauerstoff verfärbt sich die Schnittfläche gelb. Wenn keine strengen Anforderungen an die Oberflächenfarbe des Materialeinschnitts gestellt werden, ist die Verwendung von Druckluft anstelle des Stickstoffschneidens die wirtschaftlichste und praktischste Wahl. Es wird im Allgemeinen zum Schneiden von Blechteilen, Aluminiumplatten, nichtmetallischen und verzinkten Blechmaterialien verwendet. Bis zu einem gewissen Grad kann es die Oxidation reduzieren. Membran- und kostensparend ist es eine der immer häufiger eingesetzten Schneidgasquellen.

Druckluft kann direkt aus einem Luftkompressor gewonnen werden, die Luft selbst ist jedoch nicht sauber. Die Druckluft enthält große Mengen Wasser, Öl, Partikel und andere Schadstoffe. Bei verunreinigter Druckluft wird Hochdruck auf den Schutzspiegel des Laserschneidkopfes gesprüht. , verunreinigt die Schutzlinse (wie im Bild gezeigt), beeinträchtigt die Übertragung des Laserstrahls erheblich, streut den Fokus, führt dazu, dass das Produkt nicht mehr durchschneiden kann, leicht Grate bildet (wie im Bild gezeigt) usw Die Schnittfläche ist rau (wie im Bild gezeigt) und es entstehen sogar Abfallprodukte. Wenn es sich um eine Hochleistungs-Laserschneidmaschine handelt, kann es, solange sich ein sehr feiner Ölfilm oder Wassernebel auf dem Schutzspiegel oder der Düsenoberfläche befindet, dazu führen, dass der Laserkopf durch energiereiche Laseremission durchbrennt.

Daher ist kontinuierliche und stabile saubere Druckluft erforderlich, um den Schneideffekt sicherzustellen und die Laserschneidmaschine vor Schäden zu schützen. Der Indikator dafür, dass Gasanwendungen in dieser Branche die Anforderungen erfüllen können (klassifiziert nach ISO 8573-1-2010), ist derzeit, dass der Drucktaupunkt nicht unter Stufe 5 (3~7℃) liegt (im Allgemeinen der Arbeitsdruck). Bedingungen, bei denen die Temperatur das ganze Jahr über am höchsten ist, sollten außerdem berücksichtigt werden. In Gebieten, in denen die Temperatur unter Null liegt, muss der Einfluss der Temperatur auf die Druckluft berücksichtigt werden, wenn die Rohrleitung im Freien liegt oder lang ist. Der Partikelgehalt liegt nicht unter Stufe 2 und der Gesamtölgehalt liegt nicht unter Stufe 2 (